The Ultimate Guide To Alcast Company

There are several small distinctions in between functioned and cast aluminum alloys, such as that actors alloys can consist of much more significant quantities of other metals than functioned alloys. However one of the most notable distinction in between these alloys is the fabrication process whereby they will certainly most likely to provide the end product. Besides some surface area treatments, cast alloys will leave their mold and mildew in virtually the precise strong kind preferred, whereas functioned alloys will certainly go through several alterations while in their strong state.
If you believe that a functioned alloy might be the very best for your task, take an appearance at a few of our articles that explain more regarding specific functioned alloys, such as Alloy 6061 and Alloy 6063. On the various other hand, if you assume an actors alloy would be much better for you, you can discover more about some actors alloys in our Alloy 380 and Alloy 383 articles (coming soon).
The Facts About Alcast Company Uncovered
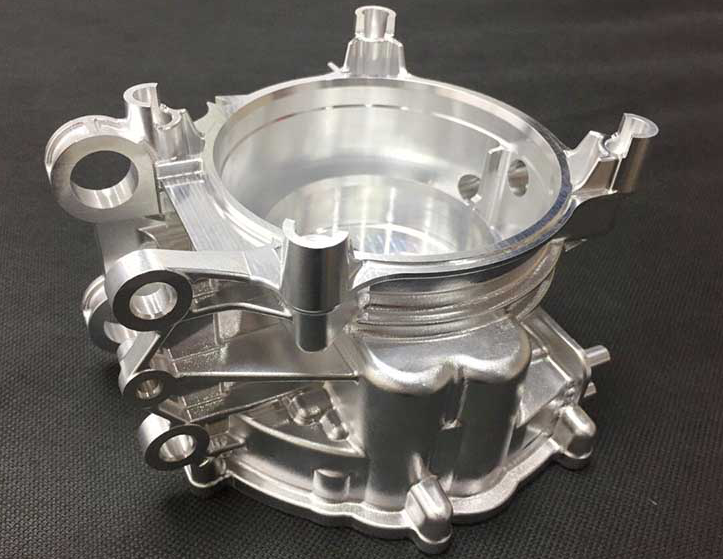
Having the experience and sector knowledge to craft your spreadings for optimum production and high quality results will certainly streamline the task. Making light weight aluminum castings needs a complicated collection of procedures to accomplish the appropriate outcomes. When picking a new light weight aluminum shop to companion with, guarantee they have extensive sector experience and are experienced concerning all facets of the light weight aluminum spreading procedure: design, manufacturing, product evaluation, and product screening.
Getting The Alcast Company To Work
By choosing a business who offers solutions that fulfill or exceed your product demands, you can be certain that your project will certainly be finished with miraculous precision and efficiency. Certain light weight aluminum foundries specialize in specific kinds of producing processes or casting methods. Various parts require various production methods to cast aluminum, such as sand casting or pass away casting.
Die spreading is the name provided to the procedure of producing intricate steel components via use of mold and mildews of the element, likewise called dies. The procedure utilizes non-ferrous steels which do not include iron, such as light weight aluminum, zinc and magnesium, due to the desirable residential properties of the steels such as reduced weight, higher conductivity, non-magnetic conductivity and resistance to deterioration.
Excitement About Alcast Company
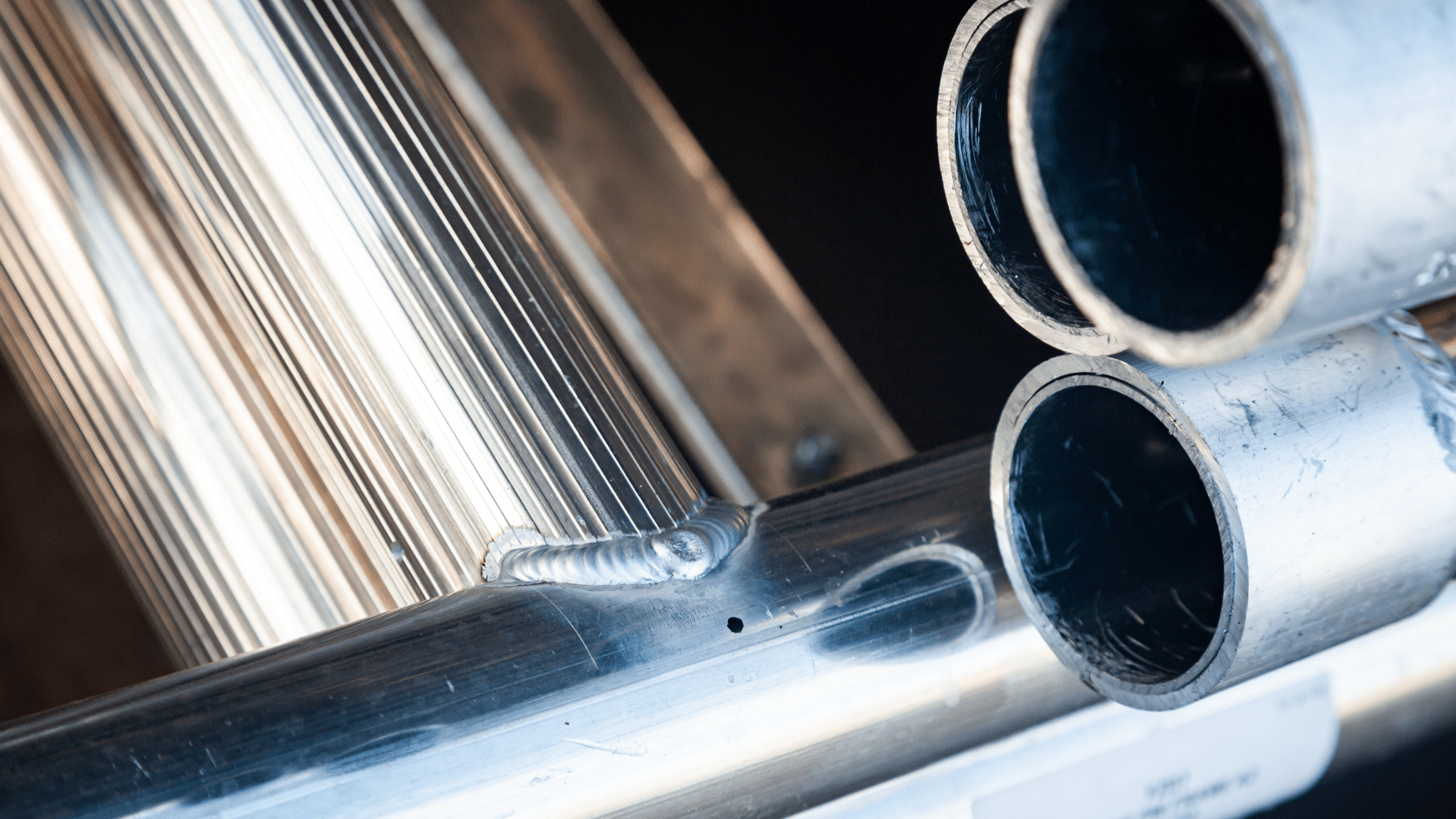
No matter the sub-process, the die casting procedure can be broken down into six actions. After the pureness of the alloy is checked, dies are developed. To prepare the dies for spreading, it is vital that the dies are tidy, to make sure that no deposit from previous manufacturings remain. After cleaning, the ejection lubrication is applied to the die to ensure a smooth release.
The pure steel, also known as ingot, is included in the heater and maintained the molten temperature of the steel, which is then moved to the shot chamber view it now and infused into the die (aluminum foundry). The stress is after that kept as the metal solidifies. When the metal solidifies, the cooling procedure starts
The 8-Minute Rule for Alcast Company
The thicker the wall surface of the component, the longer the cooling time due to the fact that of the quantity of interior metal that also needs to cool down. After the part is completely cooled, the die halves open and an ejection mechanism pushes the component out. Complying with the ejection, the die is closed for the next shot cycle.
The flash is the added product that is cast throughout the procedure. This need to be trimmed off utilizing a trim tool to leave just the main element. Deburring gets rid of the smaller sized items, called burrs, after the cutting procedure. The part is brightened, or burnished, to provide it a smooth coating.
The Best Strategy To Use For Alcast Company
Nonetheless, this proved to be an imprecise test, because the tester can cut right into a piece and miss an area with porosity. Today, leading producers use x-ray testing to see the whole inside of elements without cutting right into them. This permits them to more accurately approve or reject elements. To reach the finished product, there are 3 key alloys used as die spreading material to pick from: zinc, aluminum and magnesium.
Zinc is one of the most previously owned alloys for die spreading due to its lower price of raw products (aluminum foundry). Its rust resistance likewise permits the elements to be long long-term, and it is one of the much more castable alloys due to its lower melting factor.
Some Known Factual Statements About Alcast Company
As stated, this alloy is among the most typically utilized, yet manufactures will, sometimes, select light weight aluminum over zinc due to light weight aluminum's manufacturing advantages. Aluminum is very economical and one of the much more functional alloys. Aluminum is made use of for a variety of various products and sectors anything from window frames to aerospace products.
Comments on “Getting My Alcast Company To Work”